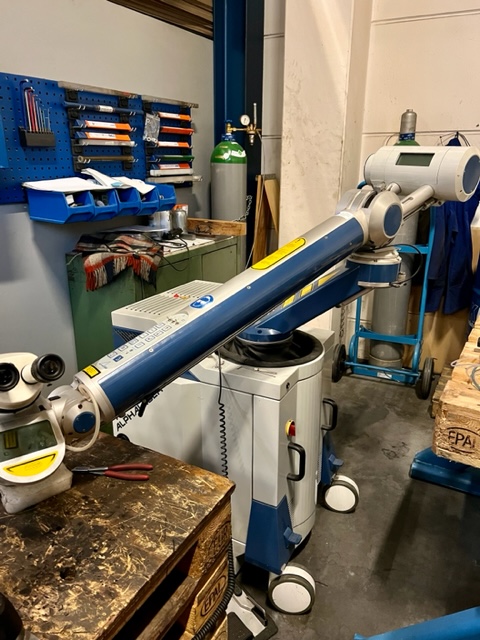
Unterschiedliche Arten von Lasern für das Schweißen in der Formenreparatur
Unterschiedliche Arten von Lasern für das Schweißen in der Formenreparatur
Einsatz von Lasertechnologie in der Formenreparatur: Eine effiziente Lösung für den Maschinenbau
Revolutionieren moderne Laser das Schweißen in der Formenbauindustrie?
Gliederung:
- Einleitung: Die Bedeutung des Laserschweißens in der Formenreparatur
- Grundlagen des Laserschweißens im Maschinenbau
- CO2-Laser in der Formenreparatur
- Nd:YAG-Laser und ihre Anwendungsvielfalt
- Faserlaser – Maximale Präzision im Maschinenbau
- Einsatz von Grünlichtlaser bei reflektierenden Materialien
- Vorteile von Diodenlaser in der Formenreparatur
- Ultrakurzpulslaser für feinste Schweißarbeiten
- Prozesskontrolle und Qualitätssicherung im Laserschweißen
- Sicherheitsaspekte im Umgang mit Lasertechnologie
- Integration von Laserschweißsystemen in die Maschinenbauprozesse
- Kosten-Nutzen-Analyse des Laserschweißens in der Formenreparatur
- FAQ Sektion zu Laserschweißen und Formenbau
- Zusammenfassung des Einsatzes von Lasertechnologie im Formenbau
- Fazit zur Bedeutung von Lasern in der Formenreparatur
- Call to Action für Formenbauer
Einleitung
Im Bereich des Maschinenbaus und speziell in der Formenreparatur spielt das Laserschweißen eine immer größere Rolle. Diese innovative Technik ermöglicht es Formenbauern, präzise und effiziente Reparaturen durchzuführen. Doch welche Lasersysteme sind am besten für die Anforderungen im Formenbau geeignet?
Hauptteil
Grundlagen des Laserschweißens im Maschinenbau
Das Laserschweißen stellt eine Schlüsseltechnologie im Maschinenbau dar, die durch den Einsatz eines Laserstrahls das Verschmelzen von Materialien an den Berührungspunkten ermöglicht.
CO2-Laser in der Formenreparatur
CO2-Laser sind insbesondere für ihre hohe Eindringtiefe bekannt und eignen sich hervorragend für die Formenreparatur im Maschinenbau, vor allem bei dickwandigen Komponenten.
Nd:YAG-Laser und ihre Anwendungsvielfalt
Nd:YAG-Laser bieten Formenbauern eine vielseitige Lösung für das Laserschweißen verschiedenster Materialien, was sie zu einem unverzichtbaren Werkzeug in der Formenreparatur macht.
Faserlaser – Maximale Präzision im Maschinenbau
Mit ihrer hohen Strahlqualität sind Faserlaser die erste Wahl für formenbauende Betriebe, die höchste Präzision beim Laserschweißen erfordern.
Einsatz von Grünlichtlaser bei reflektierenden Materialien
Grünlichtlaser schließen eine wichtige Lücke im Maschinenbau, indem sie das Schweißen von reflektierenden Materialien, die für andere Lasertypen herausfordernd sind, ermöglichen.
Vorteile von Diodenlaser in der Formenreparatur
Die Kompaktheit und Energieeffizienz von Diodenlasern macht sie zu einem gern gesehenen Werkzeug bei mobilen Reparatureinsätzen im Maschinenbau und bei der Formenreparatur.
Ultrakurzpulslaser für feinste Schweißarbeiten
Für die feinsten Schweißarbeiten im Maschinenbau, bei denen es auf minimale Wärmeeinwirkung ankommt, sind Ultrakurzpulslaser die Technologie der Wahl.
Prozesskontrolle und Qualitätssicherung im Laserschweißen
Moderne Laserschweißsysteme bieten umfassende Prozesskontrolle und tragen zur Qualitätssicherung bei, was im Maschinenbau für die Formenreparatur von höchster Bedeutung ist.
Sicherheitsaspekte im Umgang mit Lasertechnologie
Sicherheit steht an erster Stelle: Im Maschinenbau müssen beim Laserschweißen strenge Sicherheitsrichtlinien eingehalten werden.
Integration von Laserschweißsystemen in die Maschinenbauprozesse
Die Implementierung von Laserschweißtechnologie muss sorgfältig geplant werden, um eine nahtlose Integration in bestehende Fertigungsprozesse im Maschinenbau zu gewährleisten.
Kosten-Nutzen-Analyse des Laserschweißens in der Formenreparatur
Obwohl die Anfangsinvestition in Laserschweißsysteme hoch sein kann, amortisieren sich diese durch ihre Effizienz und die Qualität der Reparaturen im Formenbau.
FAQ Sektion zu Laserschweißen und Formenbau
Zusammenfassung und Fazit
Die Wahl des richtigen Lasers im Maschinenbau hängt von der spezifischen Anwendung in der Formenreparatur ab. Jede Lasertechnologie hat ihre Stärken, und die richtige Auswahl kann die Effizienz und Qualität im Formenbau erheblich steigern.
Call to Action
Sind Sie im Maschinenbau tätig und interessiert daran, Ihre Formenreparatur durch Laserschweißen zu optimieren? Kontaktieren Sie uns für eine individuelle Beratung!