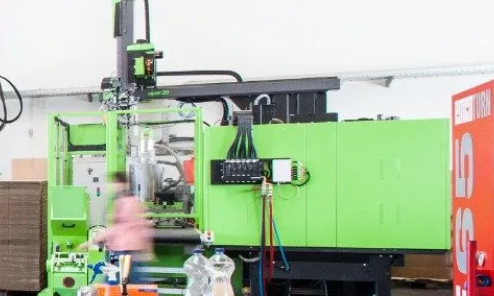
Präzisionsspritzguss für Mikroelektronik: Die Brücke zur nächsten Technologiegeneration
Präzisionsspritzguss für Mikroelektronik: Die Brücke zur nächsten Technologiegeneration
Ein Überblick über den wachsenden Bedarf und die Bedeutung des Präzisionsspritzgusses in der Mikroelektronikbranche
Einleitung
Welche Rolle spielt der Präzisionsspritzguss in der aktuellen Mikroelektroniklandschaft? Ganz einfach, er ist das verbindende Element, das es der Industrie ermöglicht, den Fortschritt zu beschleunigen und die nächste Generation von High-Tech-Geräten herzustellen. In diesem Artikel werden wir tiefer in das Thema eintauchen und verstehen, warum dieses Verfahren für den Formenbau und den Maschinenbau so entscheidend ist.
Hauptteil
Die Mikroelektronik hat in den letzten Jahrzehnten eine beispiellose Entwicklung erlebt. Dieser Fortschritt erfordert eine ständige Neuentwicklung und Verbesserung von Fertigungstechnologien. Eine dieser Schlüsseltechnologien ist der Präzisionsspritzguss.
Präzision ist der Schlüssel
Wenn es um Mikroelektronik geht, sind die Toleranzen und die erforderliche Präzision extrem eng. Die Bauteile werden immer kleiner, die Anforderungen an ihre Funktionalität jedoch immer größer. Der Präzisionsspritzguss bietet hier eine Möglichkeit, diese hohen Anforderungen zu erfüllen, da er es ermöglicht, Bauteile mit hoher Genauigkeit und Konsistenz herzustellen.
Vorteile des Präzisionsspritzgusses
Es gibt mehrere Vorteile des Präzisionsspritzgusses für die Mikroelektronik:
- Wirtschaftlichkeit: In Massenproduktion können durch den Präzisionsspritzguss erhebliche Kostenersparnisse erzielt werden.
- Schnelligkeit: Durch moderne Maschinen und Technologien können Bauteile in Sekundenschnelle hergestellt werden.
- Flexibilität: Der Prozess kann an verschiedene Materialien und Designs angepasst werden, was ihn ideal für die dynamische Welt der Mikroelektronik macht.
FAQ Sektion
1. Warum wird Präzisionsspritzguss in der Mikroelektronik so stark nachgefragt?
Da die Bauteile in der Mikroelektronik immer kleiner und komplexer werden, benötigen sie Fertigungsverfahren, die hohe Präzision und Konsistenz bieten. Der Präzisionsspritzguss erfüllt diese Anforderungen.
2. Welche Materialien werden im Präzisionsspritzguss verwendet?
Es werden verschiedene Kunststoffe und manchmal auch Metalle verwendet, je nach den spezifischen Anforderungen des Endprodukts.
3. Welche Maschinen werden im Präzisionsspritzguss eingesetzt?
Spezialisierte Spritzgussmaschinen, die für hohe Präzision und Effizienz optimiert sind, werden in diesem Prozess eingesetzt.
Zusammenfassung
Die Welt der Mikroelektronik bewegt sich rasant vorwärts, und der Präzisionsspritzguss ist eine der Schlüsseltechnologien, die es ermöglichen, mit dieser Entwicklung Schritt zu halten. Durch seine Fähigkeit, komplexe Bauteile mit hoher Präzision und Konsistenz herzustellen, stellt er eine unverzichtbare Ressource für Formenbauer und Maschinenbauer dar.
Fazit
Während die Mikroelektronik weiterhin die Grenzen des technisch Machbaren verschiebt, bleibt der Präzisionsspritzguss ein entscheidendes Bindeglied, das Innovationen zum Leben erweckt. Es ist wichtig für die Industrie, diese Technologie zu verstehen und zu nutzen, um weiterhin an der Spitze des technologischen Fortschritts zu stehen.