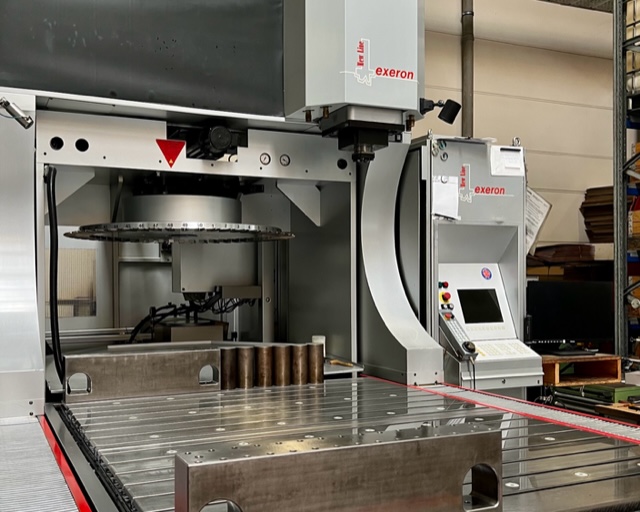
Einführung ins Senkerodieren: Eine Schritt-für-Schritt-Anleitung
Einführung ins Senkerodieren: Eine Schritt-für-Schritt-Anleitung
Das Senkerodieren hat die industrielle Landschaft revolutioniert, indem es Ingenieuren und Designern ermöglicht hat, mit einer beispiellosen Präzision zu arbeiten. Aber was genau ist Senkerodieren und wie funktioniert es?
1. Grundlagen des Senkerodierens
Senkerodieren, ein faszinierendes Verfahren der Materialbearbeitung, setzt elektrische Entladungen ein, um gezielt Material abzutragen. Der Prozess nutzt ein kontrolliertes elektrisches Feld, das zwischen einer geformten Elektrode und einem Werkstück erzeugt wird. Anstatt mechanisch Material zu entfernen, werden durch gezielte elektrische Entladungen Mikroexplosionen erzeugt, die das Material schrittweise verdampfen. Der Vorteil? Extrem feine, komplexe und präzise Formen, die sonst schwer maschinell herzustellen wären.
2. Vorbereitung des Werkstücks
Bevor man mit dem eigentlichen Erodieren beginnt, steht die sorgfältige Vorbereitung des Werkstücks an erster Stelle. Dies beinhaltet das genaue Vermessen, Reinigen und gegebenenfalls Vorbehandeln des Materials. Das Werkstück muss sicher in der Maschine befestigt werden, wobei spezielle Spannvorrichtungen zum Einsatz kommen können, um sicherzustellen, dass es während des gesamten Prozesses stabil bleibt.
3. Auswahl und Vorbereitung der Elektrode
Die Elektrode ist der Schlüssel zum Senkerodieren. Ihre Form bestimmt die Kontur des späteren Werkstücks. Während Graphit wegen seiner Beständigkeit und guten elektrischen Leitfähigkeit oft bevorzugt wird, kommen auch andere Materialien wie Kupfer in Frage. Es ist nicht nur die Wahl des richtigen Materials, sondern auch die präzise Herstellung der Elektrode, die den Unterschied ausmachen kann.
4. Einstellen der Maschinenparameter
Der Erodierprozess kann je nach Material, Dicke und gewünschtem Ergebnis variieren. Hier kommen Expertenwissen und Erfahrung ins Spiel. Eine Vielzahl von Parametern, wie Spannung, Stromstärke, Pulsfrequenz und -dauer, müssen individuell angepasst werden. Moderne Maschinen bieten oft voreingestellte Profile für gängige Materialien und Anwendungen an, was den Prozess erleichtert.
5. Starten des Erodierprozesses
Mit der richtigen Vorbereitung und Einstellung kann der eigentliche Erodierprozess beginnen. Es ist ein Ballett aus Elektrode und Werkstück, wobei Funken in kontrollierten Abständen überspringen, um das Material zu bearbeiten. Dieser Prozess erfordert ständige Überwachung, um sicherzustellen, dass alles nach Plan läuft.
6. Kontinuierliche Spülung
Das Erodieren erzeugt mikroskopisch kleine Partikel, die entfernt werden müssen. Hier kommt das Dielektrikum ins Spiel, eine spezielle Flüssigkeit, die nicht nur als Kühlmittel dient, sondern auch die Partikel fortspült und die Funkenbildung unterstützt. Ein stetiger Fluss dieser Flüssigkeit ist entscheidend, um Konsistenz und Präzision zu gewährleisten.
7. Kontrolle und Nachbearbeitung
Sobald das Erodieren abgeschlossen ist, steht die Inspektion an. Moderne Messgeräte können dabei helfen, selbst kleinste Abweichungen zu erkennen. Je nach Anforderungen kann eine Nachbearbeitung, wie Polieren oder weitere Feinarbeiten, notwendig sein.
Fazit:
Das Senkerodieren, obwohl technisch anspruchsvoll, bietet enorme Vorteile in der modernen Fertigung. Es ermöglicht nicht nur präzise und komplexe Bearbeitungen, sondern eröffnet auch neue Möglichkeiten in Design und Ingenieurwesen. Mit den richtigen Kenntnissen und einem tiefen Verständnis des Prozesses kann das Senkerodieren Wunder in der Materialbearbeitung wirken.