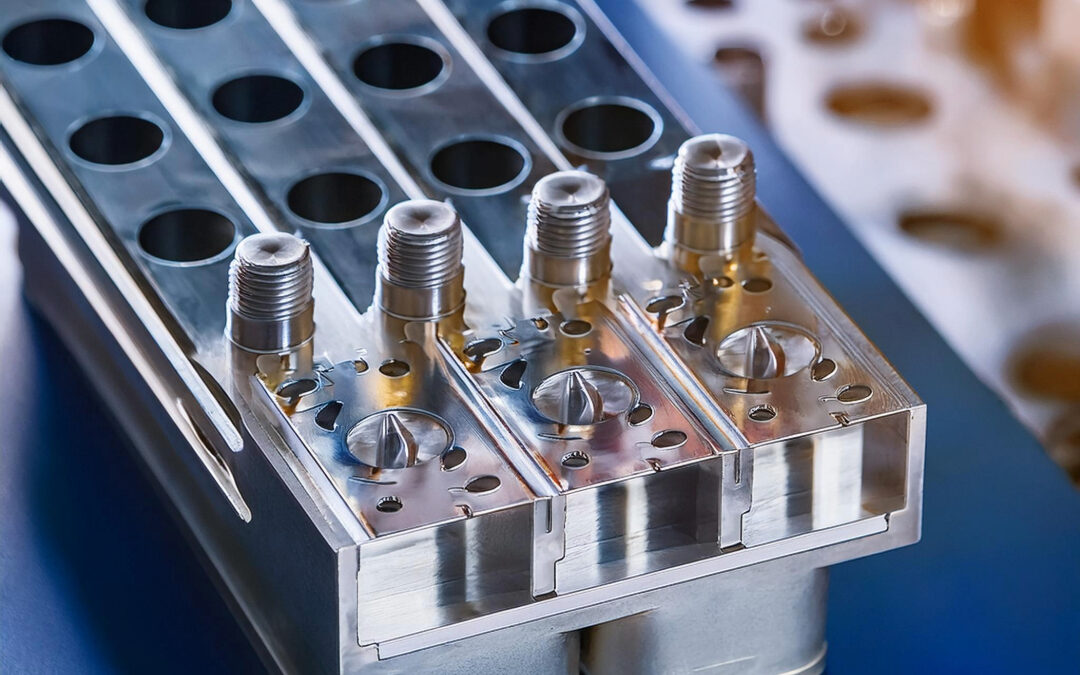
Methoden im Formenbau
Die Unterschiedlichen Methoden im Formenbau
Ein umfassender Überblick
Inhaltsverzeichnis
- Einleitung
- Gussformen
- 1 Sandguss
- 2 Kokillenguss
- 3 Druckguss
- Kunststoffspritzguss
3.1 Thermoplast-Spritzguss
3.2 Duroplast-Spritzguss
3.3 Elastomer-Spritzguss
- Pulverspritzguss
4.1 Metallpulverspritzguss
4.2 Keramikpulverspritzguss
- Extrusion
- Blasformen
- Thermoformen
- Zusammenfassung
Einleitung
Der Formenbau ist eine wesentliche Technik in der modernen Fertigungsindustrie, die es ermöglicht, Bauteile und Produkte in verschiedenen Formen und Größen herzustellen. Dieser Blogbeitrag gibt einen umfassenden Überblick über die unterschiedlichen Methoden im Formenbau, ihre Vor- und Nachteile sowie ihre spezifischen Anwendungsbereiche.
Gussformen
Sandguss
Der Sandguss ist eine traditionelle Methode des Gießens, bei der eine Form aus Sand erstellt wird. Dieses Verfahren eignet sich besonders für größere Bauteile und solche mit komplexen Geometrien. Die Hauptvorteile des Sandgusses sind die niedrigen Kosten und die Flexibilität bei der Formgebung. Ein Nachteil ist jedoch die geringere Präzision im Vergleich zu anderen Gussmethoden.
Kokillenguss
Beim Kokillenguss wird eine permanente Metallform verwendet, die wiederverwendbar ist. Diese Methode bietet eine höhere Genauigkeit und bessere Oberflächenqualität als der Sandguss. Kokillenguss wird häufig für die Herstellung von Metallteilen in großen Stückzahlen verwendet. Der Hauptnachteil dieser Methode sind die höheren Kosten für die Formherstellung.
Druckguss
Der Druckguss ist ein Verfahren, bei dem geschmolzenes Metall unter hohem Druck in eine Form gepresst wird. Diese Methode ermöglicht die Herstellung von Bauteilen mit hoher Präzision und guten mechanischen Eigenschaften. Druckguss ist besonders geeignet für die Massenproduktion von kleinen bis mittelgroßen Metallteilen. Ein Nachteil sind die hohen Investitionskosten für die Druckgussmaschinen und Formen.
Kunststoffspritzguss
Thermoplast-Spritzguss
Der Thermoplast-Spritzguss ist eine weit verbreitete Methode zur Herstellung von Kunststoffteilen. Dabei wird geschmolzener Kunststoff in eine Form gespritzt, wo er abkühlt und aushärtet. Diese Methode zeichnet sich durch kurze Zykluszeiten und hohe Wiederholgenauigkeit aus. Sie eignet sich besonders für die Massenproduktion von Kunststoffteilen. Der Hauptnachteil sind die hohen Werkzeugkosten.
Duroplast-Spritzguss
Beim Duroplast-Spritzguss werden duroplastische Kunststoffe verwendet, die nach dem Aushärten nicht mehr schmelzbar sind. Diese Methode eignet sich besonders für Anwendungen, bei denen hohe Temperaturbeständigkeit und mechanische Festigkeit erforderlich sind. Ein Nachteil ist die längere Zykluszeit im Vergleich zum Thermoplast-Spritzguss.
Elastomer-Spritzguss
Der Elastomer-Spritzguss ist ein Verfahren zur Herstellung von elastischen Kunststoffteilen. Diese Methode wird häufig für die Produktion von Dichtungen, Gummiteilen und flexiblen Komponenten eingesetzt. Die Vorteile des Elastomer-Spritzgusses sind die gute Formbarkeit und die Möglichkeit, komplexe Geometrien zu realisieren. Ein Nachteil sind die speziellen Anforderungen an die Verarbeitungstemperaturen und -drücke.
Pulverspritzguss
Metallpulverspritzguss
Der Metallpulverspritzguss kombiniert die Vorteile des Spritzgießens und der Pulvermetallurgie zur Herstellung von Metallteilen mit hoher Präzision und komplexen Geometrien. Das Verfahren eignet sich besonders für die Produktion kleiner bis mittelgroßer Teile in großen Stückzahlen. Ein Nachteil sind die hohen Materialkosten und der aufwendige Herstellungsprozess.
Keramikpulverspritzguss
Der Keramikpulverspritzguss ist ein Verfahren zur Herstellung von Keramikbauteilen mit hoher Präzision. Diese Methode wird besonders in der Elektronik- und Medizinindustrie eingesetzt, wo hohe Anforderungen an die Materialeigenschaften bestehen. Der Hauptnachteil sind die hohen Kosten für die Rohstoffe und die aufwendige Nachbearbeitung der Teile.
Extrusion
Die Extrusion ist ein kontinuierliches Verfahren zur Herstellung von Profilen und Rohren aus Kunststoff oder Metall. Dabei wird das Material durch eine formgebende Düse gedrückt und anschließend abgekühlt. Die Extrusion eignet sich besonders für die Produktion langer, gleichförmiger Bauteile. Ein Nachteil ist die begrenzte Gestaltungsmöglichkeit bei komplexen Querschnitten.
Blasformen
Das Blasformen ist ein Verfahren zur Herstellung von hohlen Kunststoffteilen, wie Flaschen und Behältern. Dabei wird ein Kunststoffschlauch in eine Form eingebracht und durch Druckluft auf die Formwände gepresst. Die Hauptvorteile des Blasformens sind die kostengünstige Produktion und die Möglichkeit, dünnwandige Hohlkörper herzustellen. Ein Nachteil sind die eingeschränkten Gestaltungsmöglichkeiten bei komplexen Formen.
Thermoformen
Das Thermoformen ist ein Verfahren zur Herstellung von Kunststoffteilen durch Erhitzen und Verformen einer Kunststoffplatte. Diese Methode wird häufig für die Produktion von Verpackungen, Behältern und technischen Teilen verwendet. Die Vorteile des Thermoformens sind die niedrigen Werkzeugkosten und die Flexibilität bei der Formgebung. Ein Nachteil ist die begrenzte Materialdicke und die geringere Präzision im Vergleich zu anderen Kunststoffverarbeitungsverfahren.
Zusammenfassung
Der Formenbau umfasst eine Vielzahl von Methoden, die jeweils spezifische Vor- und Nachteile sowie Anwendungsbereiche haben. Von traditionellen Gussverfahren wie dem Sandguss über moderne Spritzgussverfahren bis hin zu Spezialtechniken wie dem Pulverspritzguss bieten die unterschiedlichen Methoden im Formenbau Lösungen für nahezu jede Anforderung in der Fertigungsindustrie. Die Wahl der geeigneten Methode hängt von zahlreichen Faktoren ab, darunter die Materialeigenschaften, die gewünschte Präzision und die Produktionsstückzahlen. Durch die kontinuierliche Weiterentwicklung der Technologien werden die Möglichkeiten im Formenbau stetig erweitert, was zu immer effizienteren und kostengünstigeren Produktionsprozessen führt.