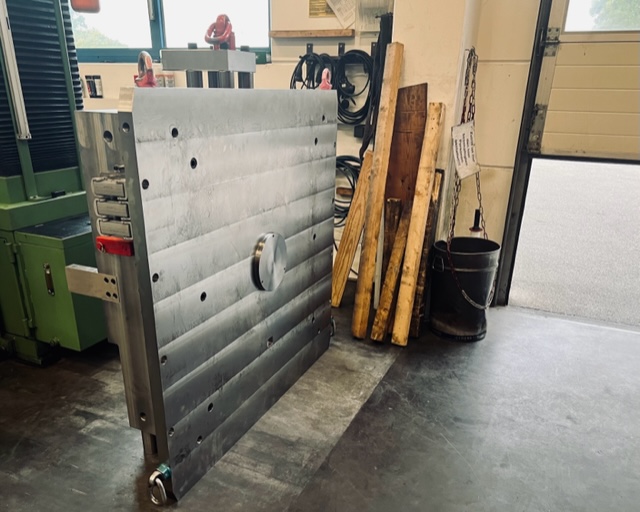
Das Zusammenspiel von Formenbau und Maschinenbau
- Die Bedeutung des Formenbaus für den Maschinenbau
- Die Zusammenarbeit zwischen Formenbau und Maschinenbau
- Die Vorteile der Zusammenarbeit
- Fazit
Das Zusammenspiel von Formenbau und Maschinenbau
Formenbau und Maschinenbau sind zwei wichtige Bereiche der Fertigungstechnik, die eng miteinander verbunden sind. Der Formenbau befasst sich mit der Herstellung von Formen und Werkzeugen, die zur Produktion von Bauteilen aus verschiedenen Materialien verwendet werden. Der Maschinenbau hingegen beschäftigt sich mit der Entwicklung, Konstruktion und Fertigung von Maschinen und Anlagen, die in der Produktion eingesetzt werden.
1. Die Bedeutung des Formenbaus für den Maschinenbau
Der Formenbau spielt eine wichtige Rolle für den Maschinenbau, da er die Grundlage für die Herstellung von präzisen und qualitativ hochwertigen Bauteilen bildet. Formen und Werkzeuge werden in verschiedenen Fertigungsverfahren eingesetzt, um Bauteile aus Metall, Kunststoff oder anderen Materialien herzustellen. Diese Bauteile werden dann in Maschinen und Anlagen verbaut, die in der Produktion eingesetzt werden.
Formen und Werkzeuge sind unerlässlich für die Herstellung von Bauteilen mit hoher Präzision und Qualität. Sie ermöglichen die Fertigung von Bauteilen mit komplexen Geometrien und engen Toleranzen. Ohne den Formenbau wäre es nicht möglich, Bauteile in der erforderlichen Qualität und Präzision herzustellen, die für den Einsatz in Maschinen und Anlagen notwendig sind.
2. Die Zusammenarbeit zwischen Formenbau und Maschinenbau
Formenbau und Maschinenbau arbeiten eng zusammen, um die Anforderungen der Produktion zu erfüllen. Der Formenbau entwickelt und fertigt Formen und Werkzeuge, die den Anforderungen des Maschinenbaus entsprechen. Der Maschinenbau wiederum nutzt diese Formen und Werkzeuge, um Bauteile herzustellen, die in Maschinen und Anlagen verbaut werden.
Die Zusammenarbeit zwischen Formenbau und Maschinenbau beginnt bereits in der Entwicklungsphase. Der Maschinenbau definiert die Anforderungen an die Bauteile, die in den Maschinen und Anlagen verbaut werden sollen. Der Formenbau entwickelt dann Formen und Werkzeuge, die diesen Anforderungen entsprechen. Dabei werden Faktoren wie die Geometrie, die Materialauswahl und die Fertigungstoleranzen berücksichtigt.
In der Fertigungsphase arbeiten Formenbau und Maschinenbau ebenfalls eng zusammen. Der Formenbau stellt die Formen und Werkzeuge bereit, die für die Fertigung der Bauteile benötigt werden. Der Maschinenbau nutzt diese Formen und Werkzeuge, um die Bauteile herzustellen. Dabei werden die Fertigungsprozesse kontinuierlich optimiert, um die Qualität der Bauteile zu verbessern und die Produktionskosten zu senken.
3. Die Vorteile der Zusammenarbeit
Die Zusammenarbeit zwischen Formenbau und Maschinenbau bringt viele Vorteile mit sich. Durch die enge Abstimmung können Formen und Werkzeuge präzise an die Anforderungen des Maschinenbaus angepasst werden. Dies führt zu einer höheren Qualität der hergestellten Bauteile und einer effizienteren Produktion. Zudem können durch die Zusammenarbeit Kosten gesenkt und die Produktivität gesteigert werden.
Ein weiterer Vorteil der Zusammenarbeit ist die Möglichkeit, innovative Lösungen zu entwickeln. Durch die enge Zusammenarbeit können Formenbau und Maschinenbau gemeinsam neue Fertigungsverfahren und Materialien erforschen und entwickeln. Dies ermöglicht die Herstellung von Bauteilen mit verbesserten Eigenschaften und die Erschließung neuer Anwendungsbereiche.
Fazit
Formenbau und Maschinenbau sind zwei wichtige Bereiche der Fertigungstechnik, die eng miteinander verbunden sind. Durch die enge Zusammenarbeit können Formen und Werkzeuge präzise an die Anforderungen des Maschinenbaus angepasst werden, was zu einer höheren Qualität der hergestellten Bauteile und einer effizient
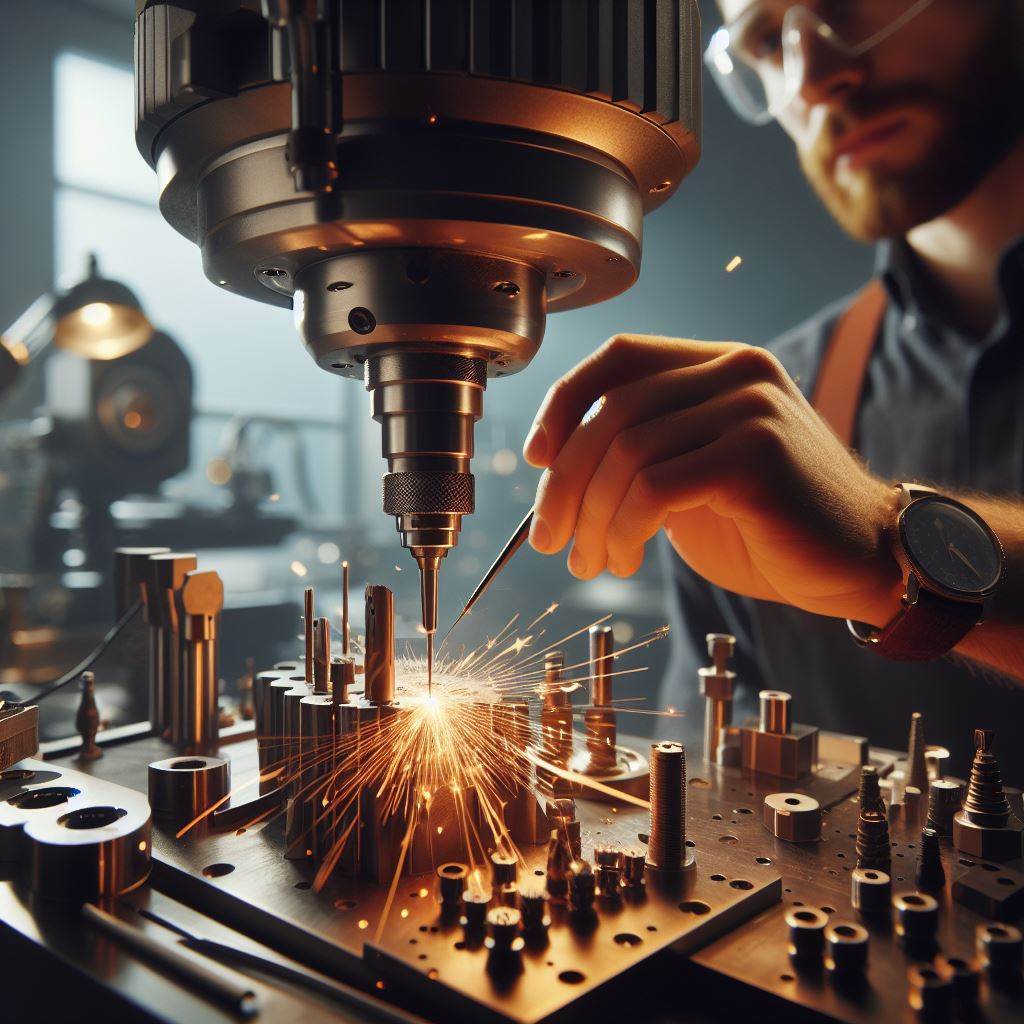